Understanding the Landscape of CNC Lathe Machining Parts Manufacturing in China
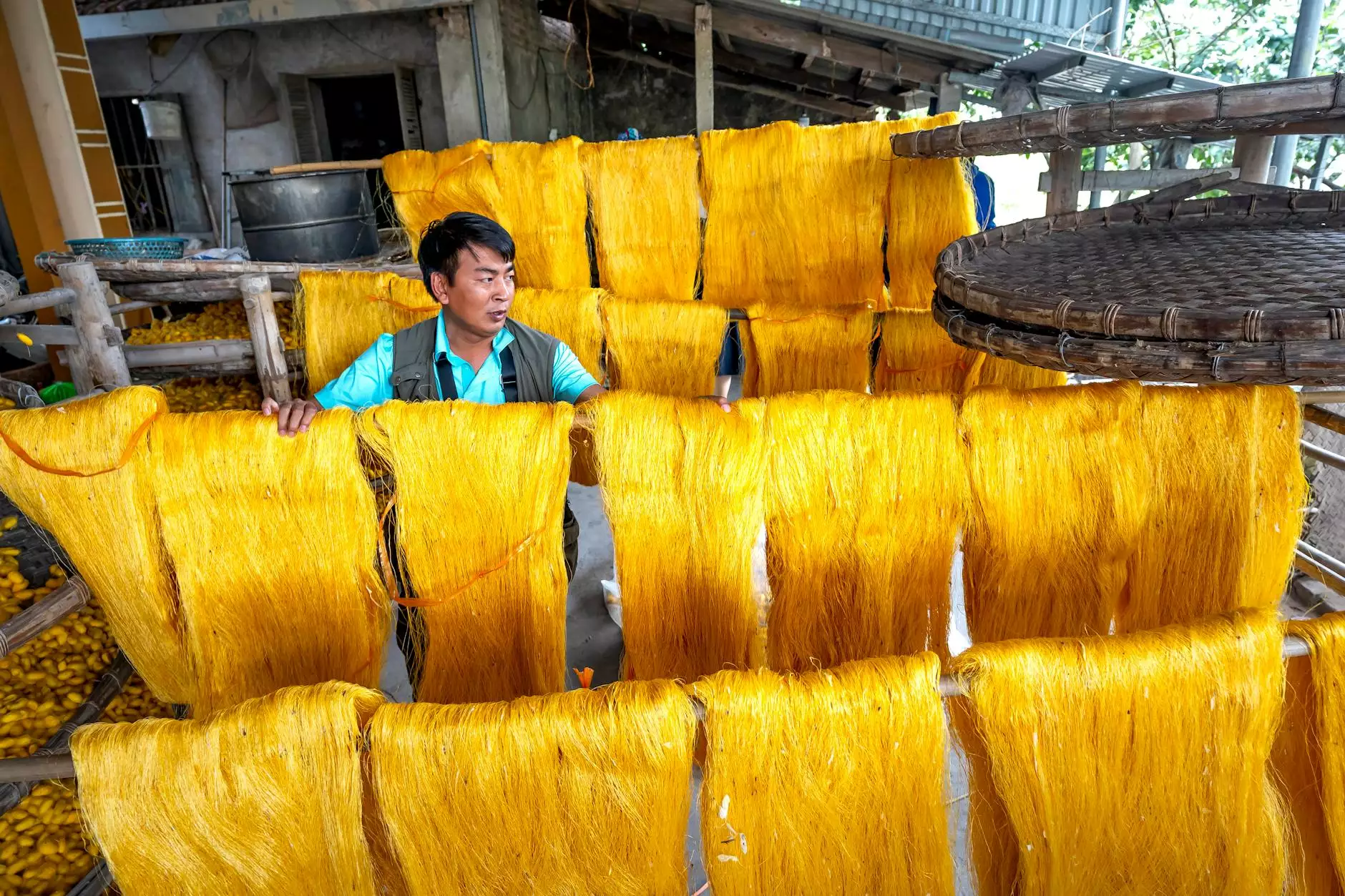
In today's rapidly evolving manufacturing environment, China has established itself as a dominant player in the field of CNC lathe machining parts manufacturing. As industries worldwide seek precision, efficiency, and cost-effectiveness, the role of a China CNC lathe machining parts manufacturer has become more critical than ever. In this article, we will delve into the various aspects of this industry, the technologies employed, and why businesses across the globe are increasingly turning to Chinese manufacturers for their CNC machining needs.
The Significance of CNC Lathe Machining
CNC lathe machining is a precise manufacturing process that uses computer-controlled machines to shape materials into desired forms. This technique is essential for producing intricate parts with high accuracy, making it indispensable in industries such as automotive, aerospace, electronics, and medical devices. The demand for precision-engineered components has heightened, encouraging manufacturers to innovate continually.
Key Advantages of CNC Machining
- High Precision: CNC machines are capable of achieving tight tolerances and high repeatability, ensuring products are manufactured with exceptional accuracy.
- Efficiency: Automated processes reduce production time significantly, allowing manufacturers to meet tight deadlines and fulfill large orders quickly.
- Flexibility: CNC machines can be programmed to produce a wide variety of parts, enabling manufacturers to adapt quickly to market demands.
- Cost-Effectiveness: While initial investments in CNC machinery can be high, the long-term savings in labor and material costs make it a financially viable option.
Why Choose a China CNC Lathe Machining Parts Manufacturer?
The question often arises: why should a business opt for a China CNC lathe machining parts manufacturer for their machining needs? The reasons are abundant, and they underscore China's growing reputation in global manufacturing.
1. Competitive Pricing
One of the most compelling reasons to partner with a Chinese manufacturer is cost. China’s vast workforce and established supply chains allow for lower production costs without compromising on quality. Economies of scale come into play, where the more units produced, the lower the cost per unit becomes, making it incredibly advantageous for companies looking to optimize their budgets.
2. Technological Advancements
Chinese manufacturers have not only invested heavily in the latest CNC technologies but have also focused on implementing Industry 4.0 practices. This commitment to modernization ensures that they produce components that meet international standards. Advanced machinery and software enhance precision and efficiency, making them a preferred supplier for many companies.
3. Skilled Workforce
An essential component of successful manufacturing is the workforce behind it. In China, the combination of a large pool of skilled engineers and technicians trained in modern machining practices means that businesses can expect high-quality output. Continuous training and an emphasis on development ensure that this expertise is preserved and advanced.
4. Robust Supply Chains
China's infrastructure has been a pivotal factor in its manufacturing success. A well-established logistics network aids efficient delivery of raw materials and finished products. This smooth operation translates into shorter lead times, which is critical for businesses aiming to stay competitive and responsive to market changes.
5. Customization Capabilities
A significant advantage of partnering with a China CNC lathe machining parts manufacturer is the ability to customize orders. CNC machining allows for specific modifications to be made during production, accommodating unique specifications required by clients. This level of customization is imperative in fields such as aerospace or medical equipment, where precision is non-negotiable.
The Manufacturing Process: From Design to Delivery
The journey of creating CNC lathe machined parts involves several critical steps. Understanding this process helps businesses appreciate the intricacies involved and reinforces confidence in their manufacturing partners.
1. Design and Prototyping
The first step in CNC machining is the design phase, where precise specifications are developed, often including the use of CAD (Computer-Aided Design) software. During this stage, prototypes may be created to ensure the design's functionality and efficacy before full-scale production begins.
2. Programming the CNC Machine
Once the design is finalized, the next step is to convert the CAD files into a format that CNC machines can understand. This programming is critical, as it dictates the machine's movements and the machining processes that will be executed. Skilled programmers play an important role here, ensuring that each detail is accounted for.
3. Material Selection
Different projects require different materials. China CNC lathe machining parts manufacturers offer a wide array of materials, including metals, plastics, and composites. The choice of material can affect functionality, cost, and production speed, making the decision a key factor in the manufacturing process.
4. Machining Operations
This phase involves the actual machining operations, where the CNC lathe machine shapes the material according to the specifications laid out in the programming stage. This precision ensures that components are produced with minimal waste and maximum efficiency.
5. Quality Control and Assurance
Quality is paramount in CNC machining, particularly when parts are utilized in critical applications. Comprehensive quality control measures are implemented throughout the manufacturing process. Inspections are conducted at various stages to ensure adherence to specifications and standards.
Emerging Trends in CNC Machining in China
As technology continues to evolve, so do the practices and capabilities of CNC lathe machining in China. Staying informed about these trends is essential for businesses seeking to maintain a competitive edge.
1. Automation and Robotics
The integration of robotics into CNC machining processes enhances productivity and reduces human error. Automation not only speeds up production times but also allows for consistent quality in manufacturing.
2. IoT and Smart Manufacturing
The Internet of Things (IoT) is transforming CNC machining, enabling machines to communicate with each other and with human operators. This connectivity allows for better monitoring of machine performance, predictive maintenance, and streamlined operations.
3. Sustainable Manufacturing
As global awareness of environmental issues grows, Chinese manufacturers are also making strides towards more sustainable practices. This includes reducing waste in machining processes, optimizing energy use, and exploring alternative materials.
Conclusion: The Future of CNC Lathe Machining Parts Manufacturing in China
The China CNC lathe machining parts manufacturer ecosystem is poised for continued growth and innovation. With their ability to offer competitive pricing, advanced technologies, and skilled labor, Chinese manufacturers will remain a cornerstone for businesses in need of high-quality machined parts.
Whether you are in the automotive, aerospace, or medical field, leveraging the capabilities of China's CNC lathe machining experts can lead you to achieve your manufacturing goals more efficiently. As technology and practices evolve, China’s CNC machining sector will undoubtedly adapt, providing even greater value to international businesses seeking to remain competitive in a fast-paced market.
For further insights into partnering with a trusted China CNC lathe machining parts manufacturer, visit deepmould.net, where you can explore a range of services designed to cater to your unique machining needs.